Metody powlekania fotomaski są ogólnie podzielone na powlekanie wirowe, powlekanie zanurzeniowe i powlekanie rolkowe, spośród których najczęściej stosowane jest powlekanie wirowe. Podczas powlekania wirowego fotomaska jest nakraplana na podłoże, a podłoże można obracać z dużą prędkością, aby uzyskać warstwę fotorezystu. Następnie można uzyskać stały film, podgrzewając go na gorącej płycie. Powłoka wirowa nadaje się do powlekania od ultracienkich folii (około 20 nm) do grubych folii o grubości około 100um. Charakteryzuje się dobrą jednorodnością, jednolitą grubością warstwy pomiędzy płytkami, niewielką liczbą defektów itp. oraz można uzyskać powłokę o wysokiej wydajności powlekania.
Proces powlekania wirowego
Podczas powlekania wirowego główna prędkość obrotowa podłoża określa grubość warstwy fotomaski. Zależność pomiędzy prędkością obrotową a grubością folii jest następująca:
Spin=kTn
We wzorze Spin oznacza prędkość obrotową; T jest grubością folii; k i n są stałymi.
Czynniki wpływające na proces powlekania wirowego
Chociaż grubość folii zależy od głównej prędkości obrotowej, jest ona również powiązana z temperaturą pokojową, wilgotnością, lepkością fotorezystu i rodzajem fotorezystu. Porównanie różnych typów krzywych powłok fotorezystowych pokazano na rysunku 1.
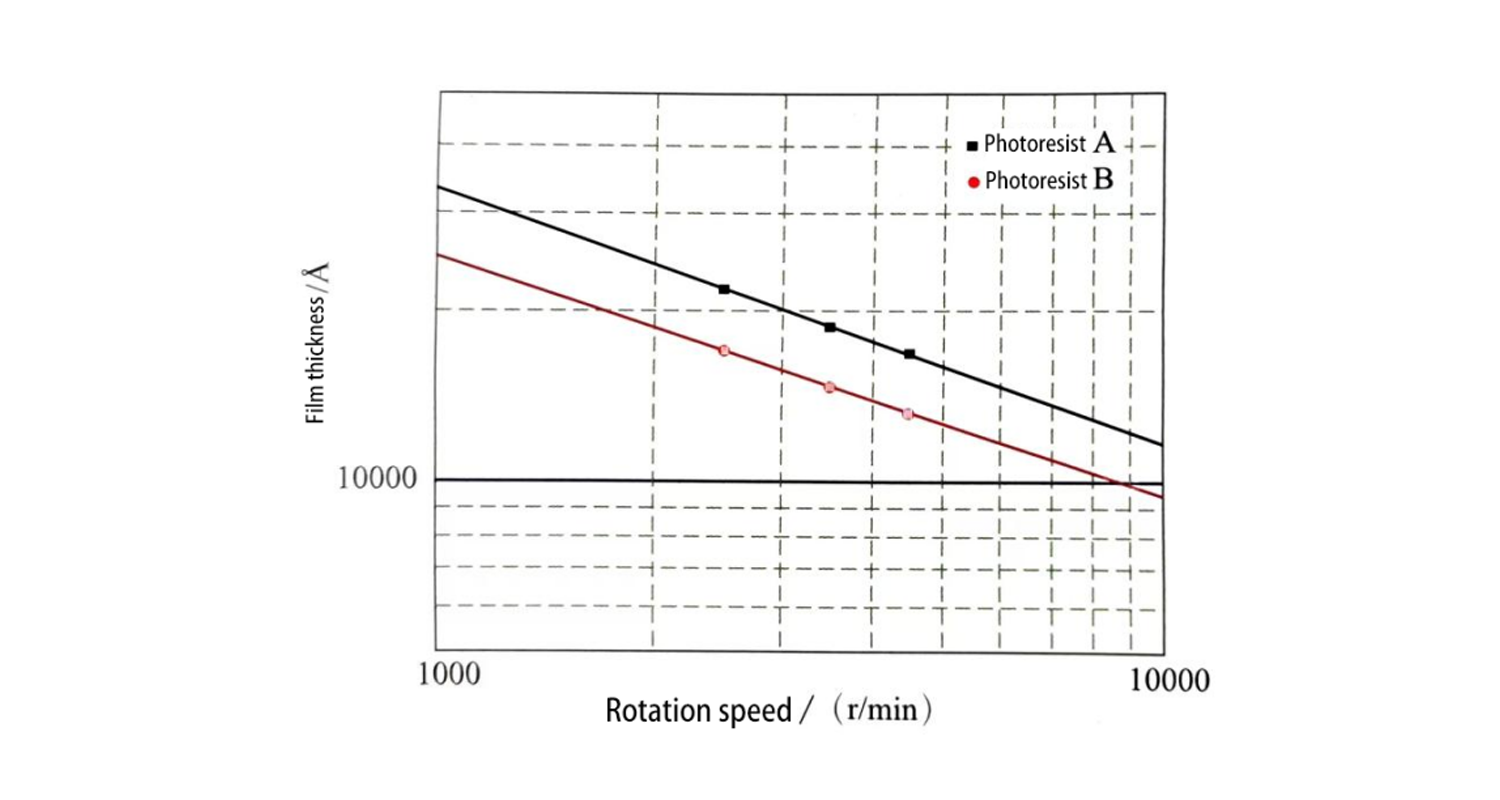
Rysunek 1: Porównanie różnych typów krzywych powłok fotomaskowych
Wpływ czasu obrotu głównego
Im krótszy czas obrotu głównego, tym grubsza jest folia. Im większy jest czas obrotu głównego, tym cieńsza staje się folia. Gdy przekracza 20 s, grubość warstwy pozostaje prawie niezmieniona. Dlatego główny czas rotacji jest zwykle wybierany na więcej niż 20 sekund. Zależność pomiędzy czasem obrotu głównego a grubością folii przedstawiono na rysunku 2.
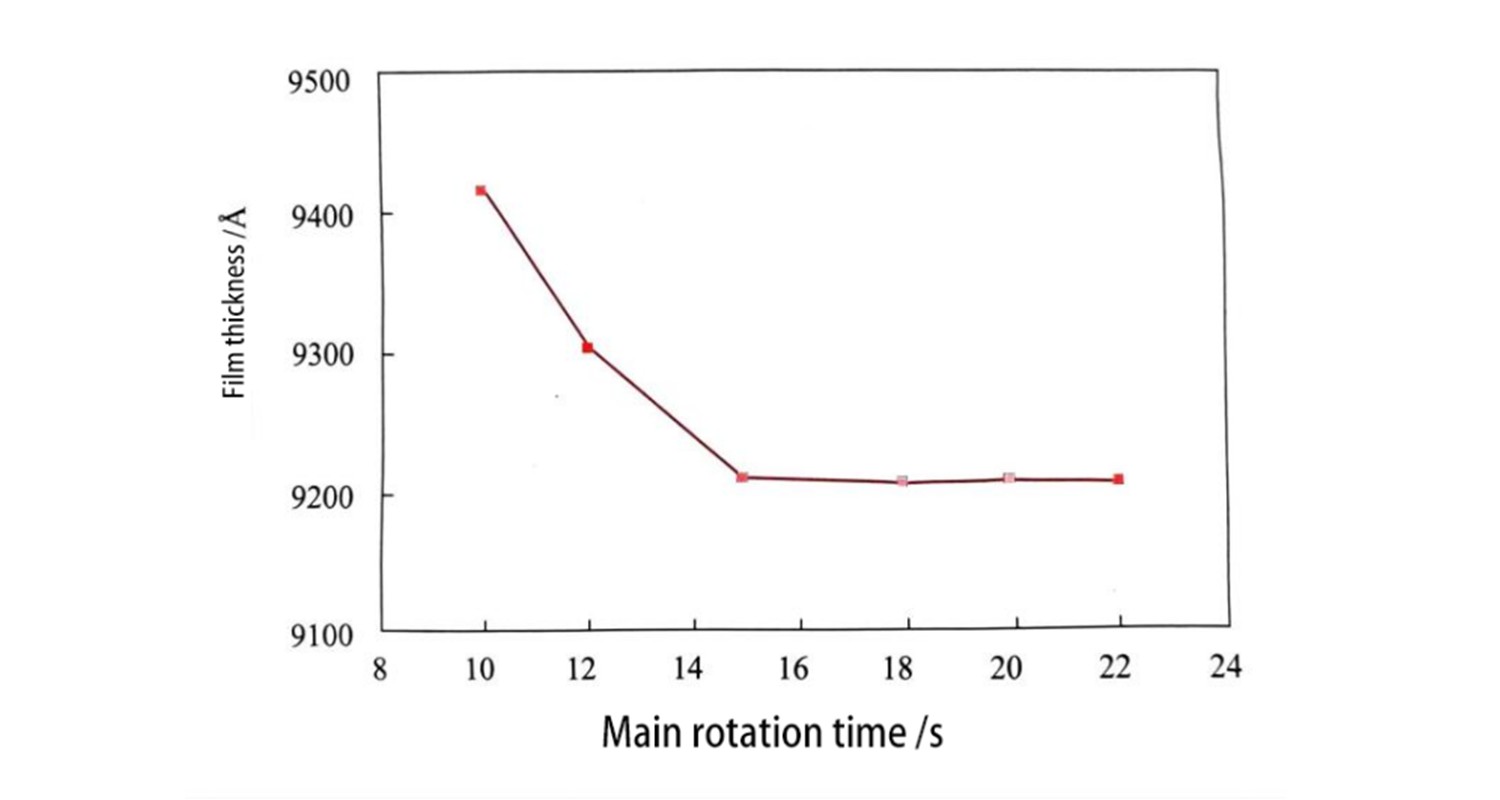
Rysunek 2: Zależność pomiędzy czasem obrotu głównego a grubością warstwy
W przypadku nakraplania fotorezystu na podłoże, nawet jeśli późniejsza główna prędkość obrotowa jest taka sama, prędkość obrotowa podłoża podczas kapania będzie miała wpływ na ostateczną grubość warstwy. Grubość warstwy fotorezystu wzrasta wraz ze wzrostem prędkości obrotowej podłoża podczas kapania, co wynika z wpływu odparowania rozpuszczalnika podczas rozkładania fotomaski po kapaniu. Rysunek 3 przedstawia zależność pomiędzy grubością folii a główną prędkością obrotową przy różnych prędkościach obrotowych podłoża podczas kapania fotorezystu. Z rysunku widać, że wraz ze wzrostem prędkości obrotowej ociekającego podłoża grubość warstwy zmienia się szybciej, a różnica jest bardziej widoczna w obszarze o niższej głównej prędkości obrotowej.
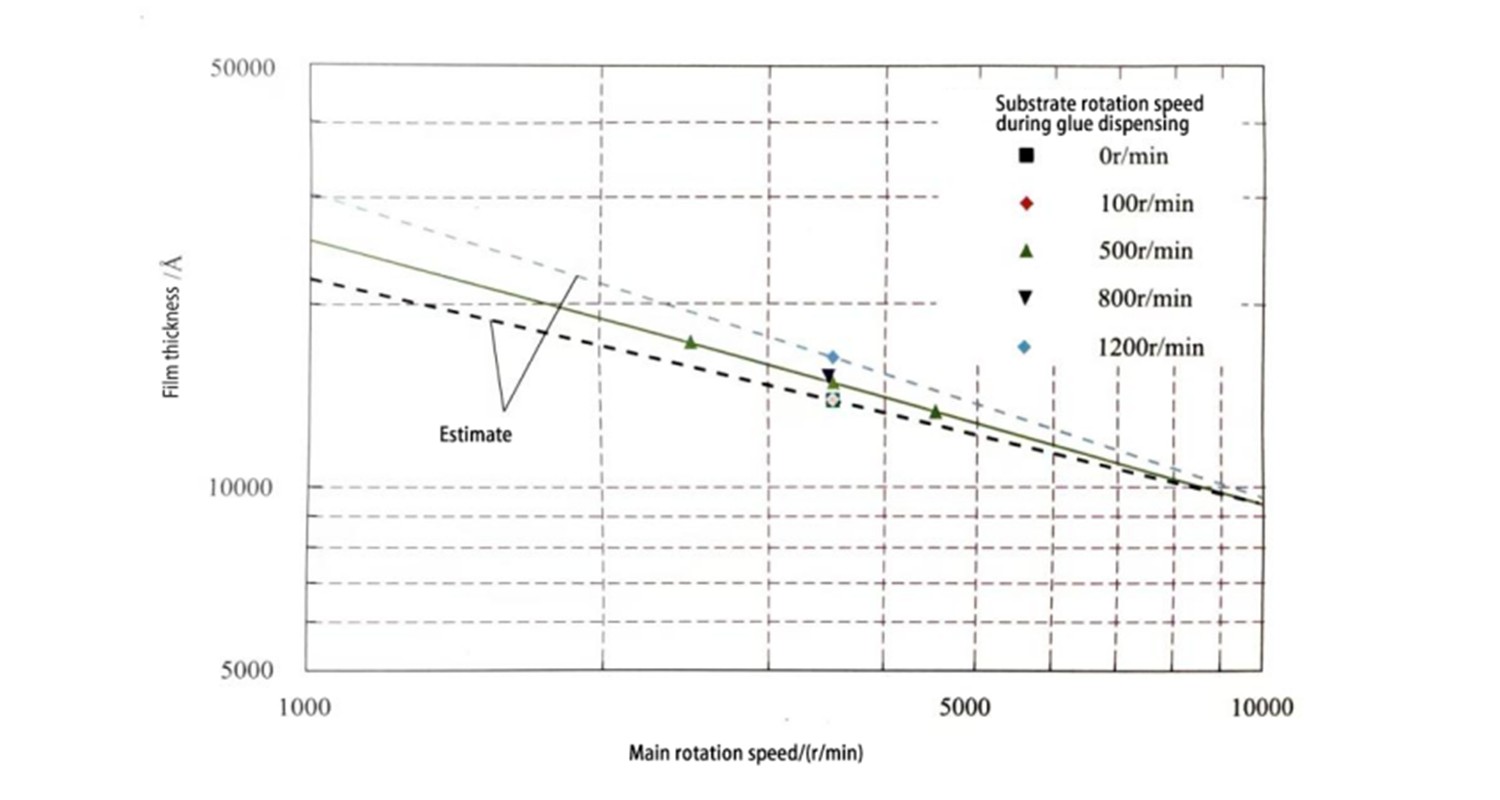
Rysunek 3: Zależność pomiędzy grubością folii a główną prędkością obrotową przy różnych prędkościach obrotowych podłoża podczas dozowania fotorezystu
Wpływ wilgoci podczas powlekania
Gdy wilgotność spada, grubość warstwy wzrasta, ponieważ spadek wilgotności sprzyja odparowaniu rozpuszczalnika. Jednakże rozkład grubości folii nie zmienia się znacząco. Rysunek 4 pokazuje zależność pomiędzy wilgotnością i rozkładem grubości powłoki podczas powlekania.
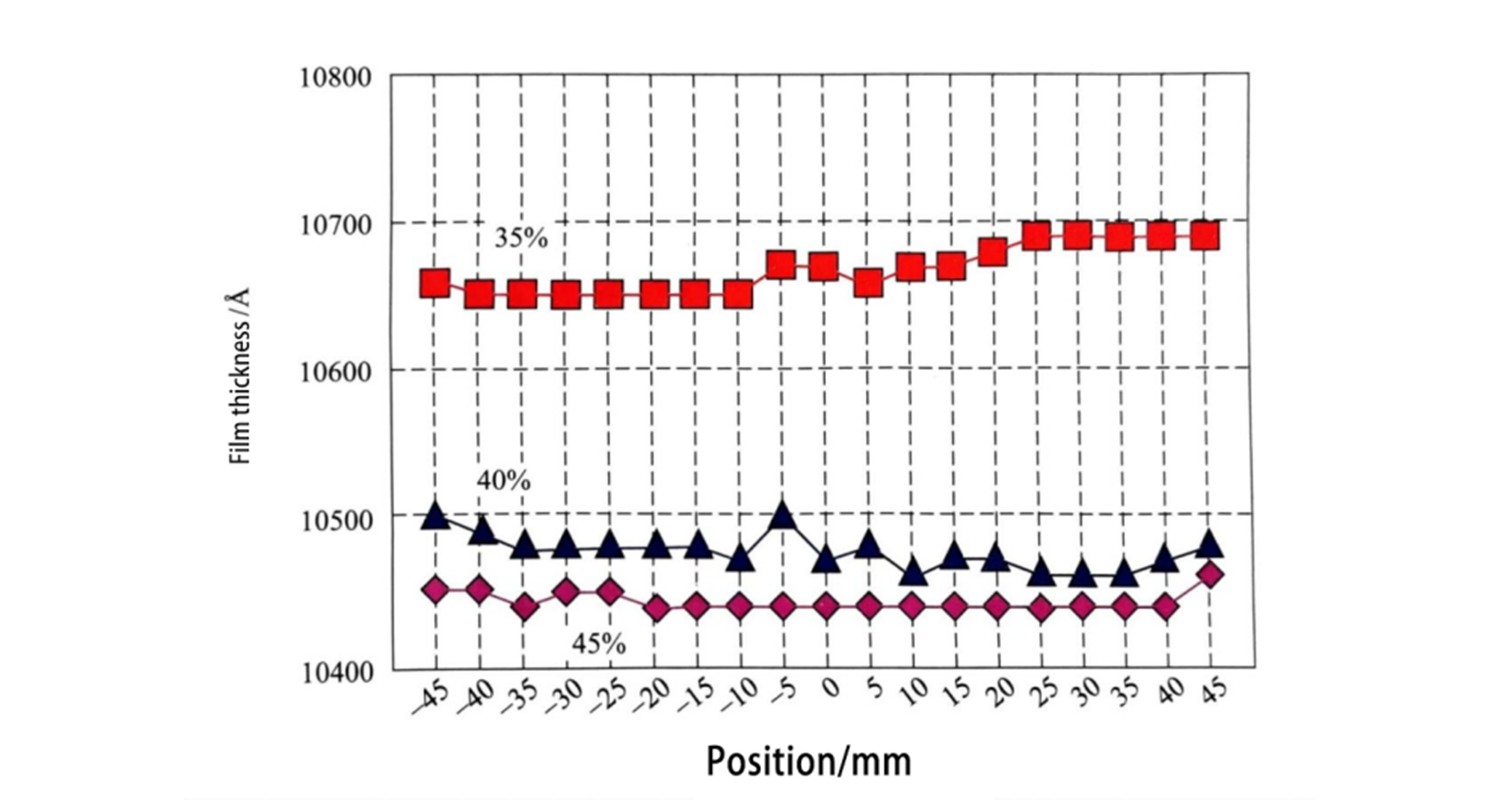
Rysunek 4: Zależność pomiędzy wilgotnością i rozkładem grubości powłoki podczas powlekania
Wpływ temperatury podczas powlekania
Wraz ze wzrostem temperatury w pomieszczeniu zwiększa się grubość powłoki. Z rysunku 5 można zobaczyć, że rozkład grubości warstwy fotorezystu zmienia się z wypukłego na wklęsły. Krzywa na rysunku pokazuje również, że największą jednorodność uzyskuje się, gdy temperatura w pomieszczeniu wynosi 26°C, a temperatura fotomaski wynosi 21°C.
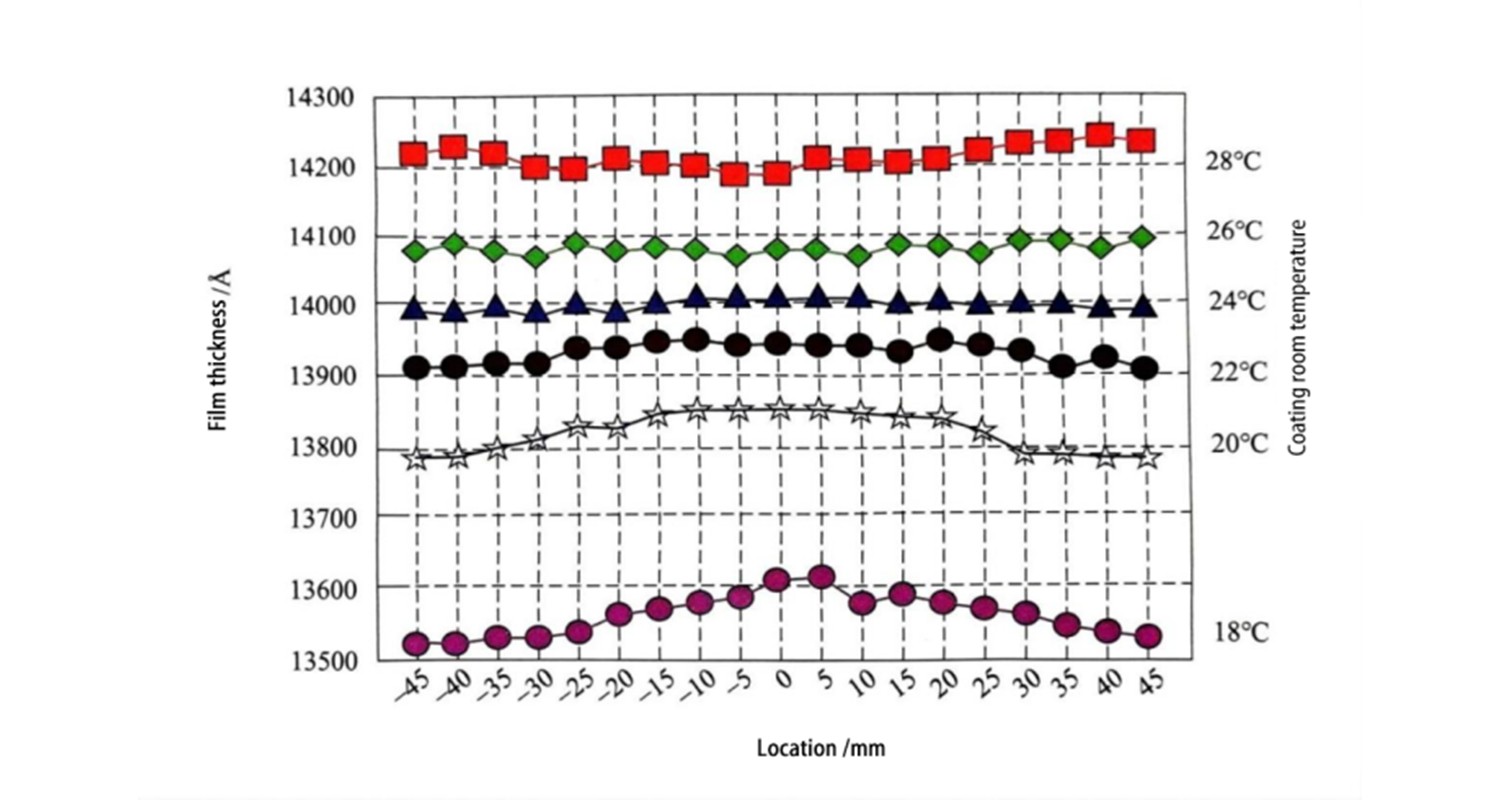
Rysunek 5: Zależność pomiędzy rozkładem temperatury i grubości powłoki podczas powlekania
Wpływ prędkości spalin podczas powlekania
Rysunek 6 przedstawia zależność pomiędzy prędkością spalin a rozkładem grubości folii. W przypadku braku wydechu widać, że środek płytki ma tendencję do gęstnienia. Zwiększenie prędkości wydechu poprawi równomierność, ale jeśli zostanie zwiększona zbyt mocno, równomierność zmniejszy się. Można zauważyć, że istnieje optymalna wartość prędkości spalin.
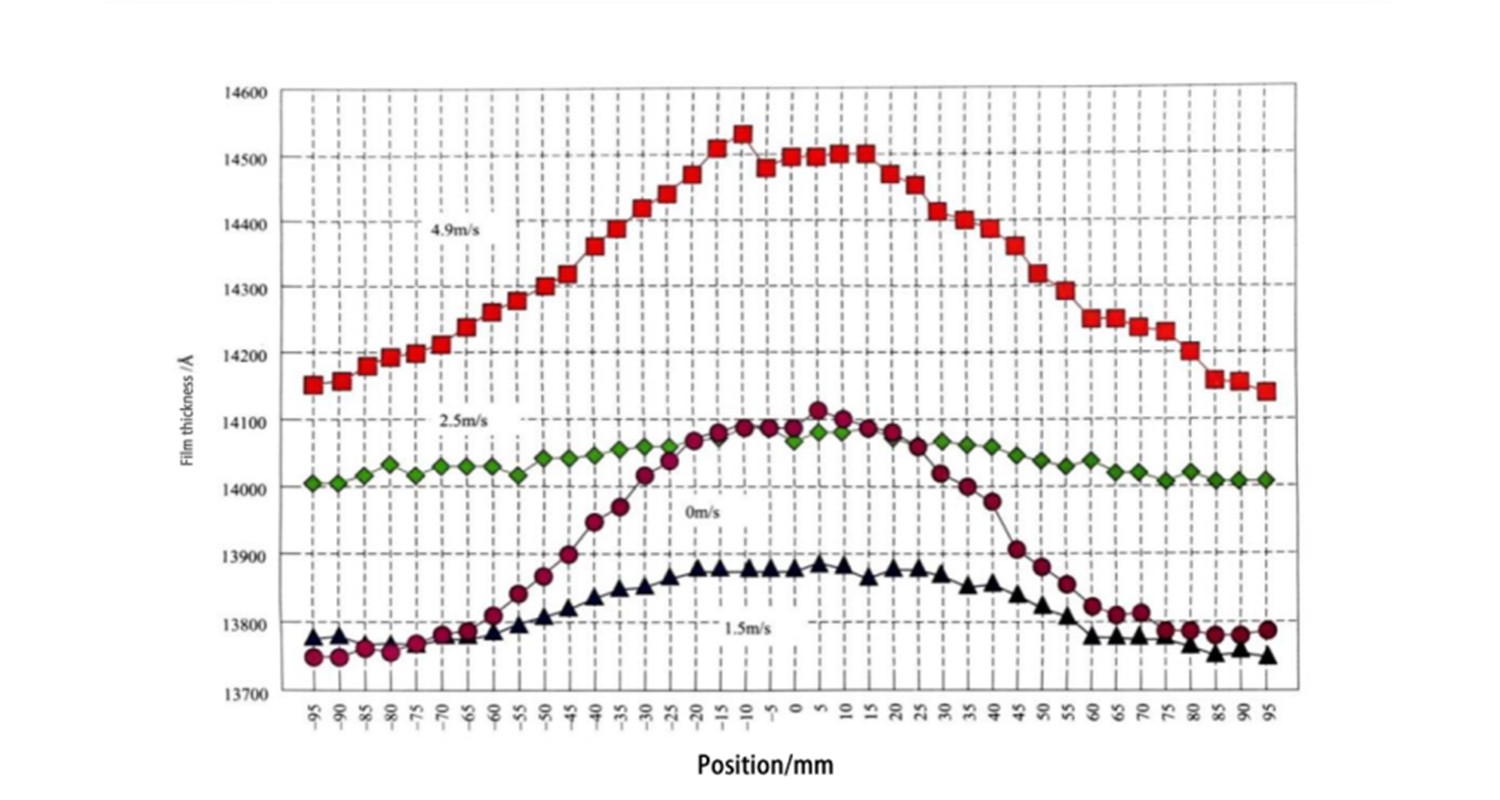
Rysunek 6: Zależność pomiędzy prędkością spalin a rozkładem grubości folii
Leczenie HMDS
Aby fotomaska była łatwiejsza do powlekania, płytkę należy potraktować heksametylodisilazanem (HMDS). Zwłaszcza gdy wilgoć zwiąże się z powierzchnią warstwy tlenku krzemu, tworzy się silanol, który zmniejsza przyczepność fotomaski. W celu usunięcia wilgoci i rozłożenia silanolu, płytkę zazwyczaj podgrzewa się do temperatury 100-120°C i wprowadza się mgłę HMDS w celu wywołania reakcji chemicznej. Mechanizm reakcji pokazano na rysunku 7. Dzięki obróbce HMDS powierzchnia hydrofilowa o małym kącie zwilżania staje się powierzchnią hydrofobową o dużym kącie zwilżania. Ogrzewanie płytki może uzyskać większą przyczepność fotorezystu.
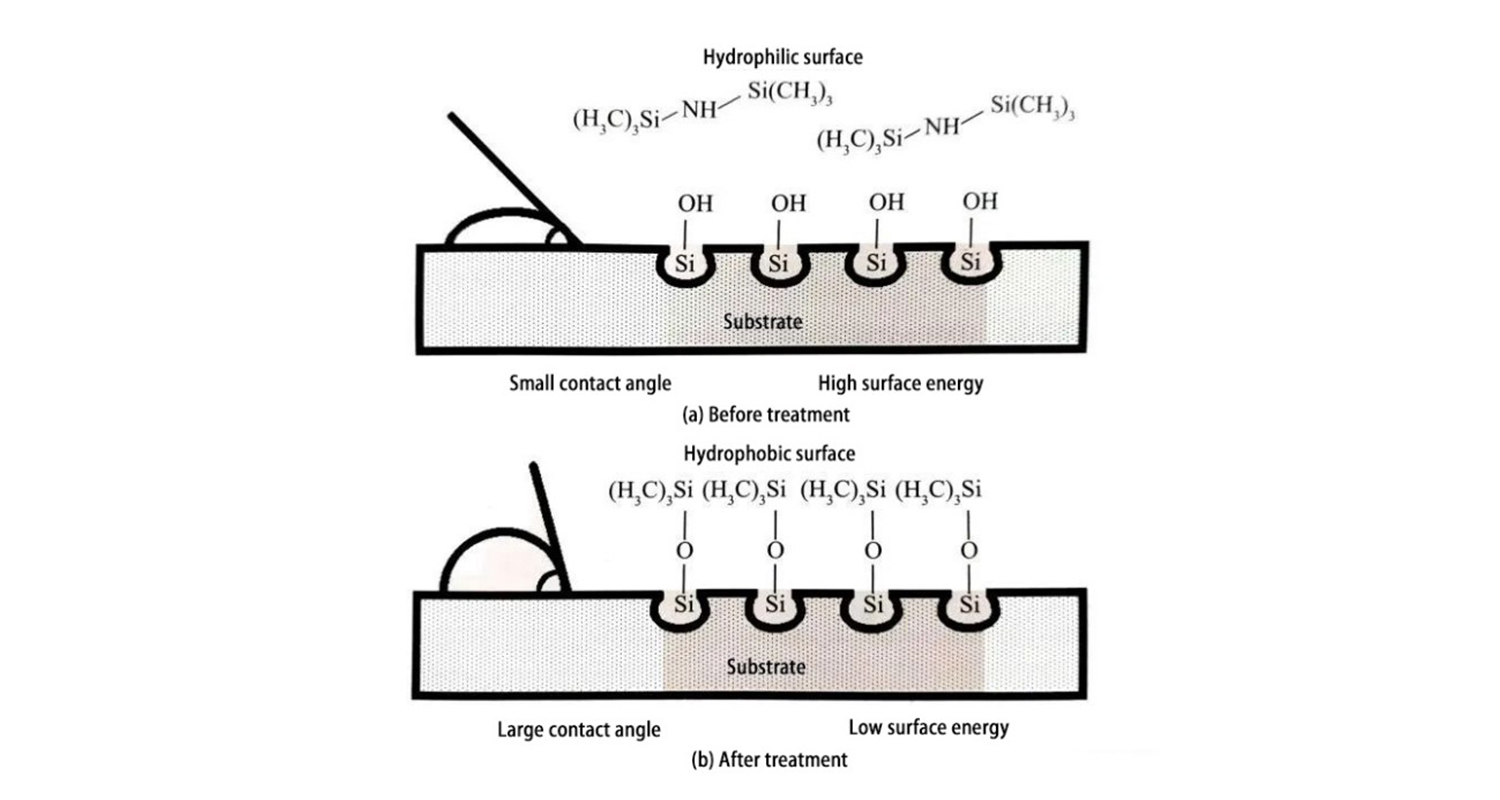
Rysunek 7: Mechanizm reakcji HMDS
Efekt obróbki HMDS można zaobserwować mierząc kąt zwilżania. Figura 8 przedstawia zależność pomiędzy czasem obróbki HMDS i kątem zwilżania (temperatura obróbki 110°C). Podłoże to Si, czas obróbki HMDS jest większy niż 1 minuta, kąt zwilżania jest większy niż 80°, a efekt obróbki jest stabilny. Figura 9 przedstawia zależność pomiędzy temperaturą obróbki HMDS i kątem zwilżania (czas obróbki 60 s). Gdy temperatura przekracza 120 ℃, kąt zwilżania maleje, co wskazuje, że HMDS rozkłada się pod wpływem ciepła. Dlatego obróbkę HMDS zwykle przeprowadza się w temperaturze 100-110℃.
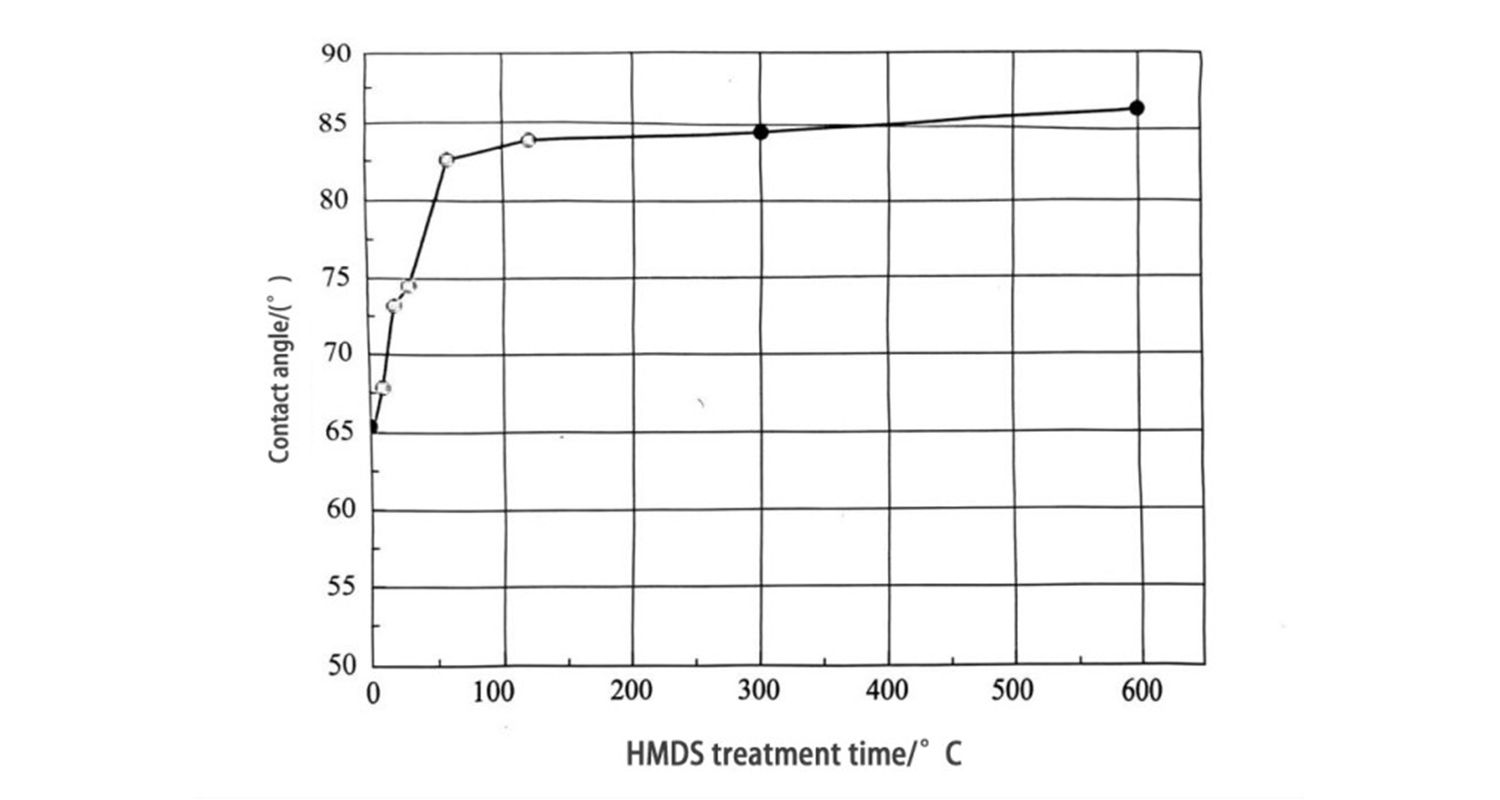
Rysunek 8: Zależność pomiędzy czasem leczenia HMDS
i kąt zwilżania (temperatura obróbki 110℃)
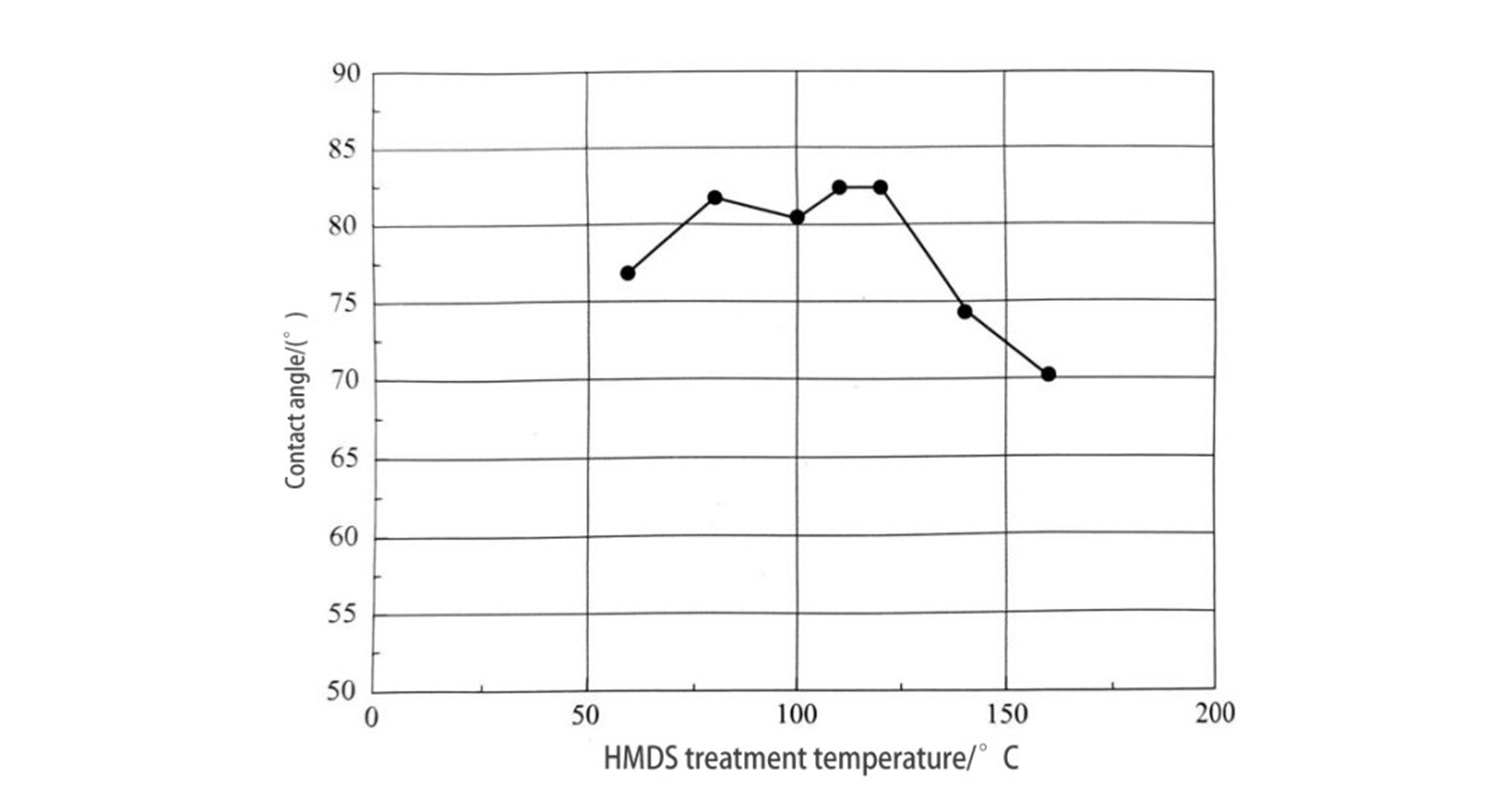
Rysunek 9: Zależność pomiędzy temperaturą obróbki HMDS a kątem zwilżania (czas obróbki 60 s)
Obróbkę HMDS przeprowadza się na podłożu krzemowym z warstwą tlenku, tworząc wzór fotomaski. Następnie warstwę tlenkową trawi się kwasem fluorowodorowym z dodatkiem buforu i stwierdza się, że po obróbce HMDS można zapobiec odpadaniu wzoru fotorezystu. Rycina 10 przedstawia efekt obróbki HMDS (wielkość wzoru wynosi 1 um).
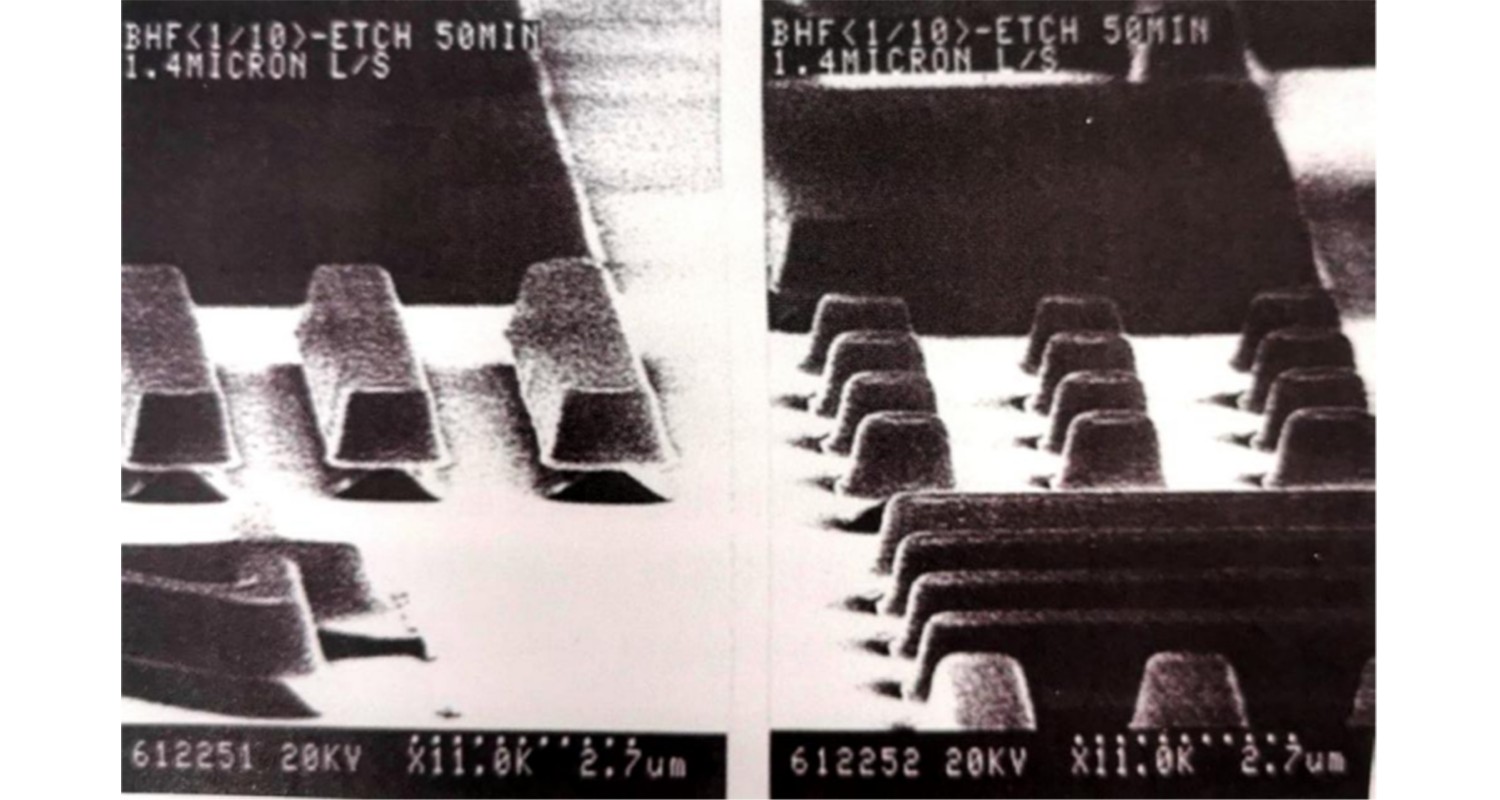
Rysunek 10: Efekt leczenia HMDS (rozmiar wzoru to 1um)
Wstępne pieczenie
Przy tej samej prędkości obrotowej, im wyższa temperatura wstępnego wypalania, tym mniejsza grubość folii, co oznacza, że im wyższa temperatura wstępnego wypalania, tym więcej rozpuszczalnika odparowuje, co skutkuje cieńszą grubością folii. Rycina 11 przedstawia zależność pomiędzy temperaturą przed pieczeniem a parametrem A Dilla. Parametr A wskazuje stężenie środka światłoczułego. Jak widać na rysunku, gdy temperatura wstępnego wypieku wzrośnie powyżej 140°C, parametr A maleje, co wskazuje, że środek światłoczuły rozkłada się w wyższej temperaturze. Figura 12 przedstawia transmitancję widmową w różnych temperaturach przed pieczeniem. W temperaturze 160°C i 180°C można zaobserwować wzrost przepuszczalności w zakresie długości fal 300-500nm. Potwierdza to, że środek światłoczuły ulega wypaleniu i rozkładowi w wysokich temperaturach. Temperatura wstępnego pieczenia ma wartość optymalną, o której decydują właściwości świetlne i czułość.
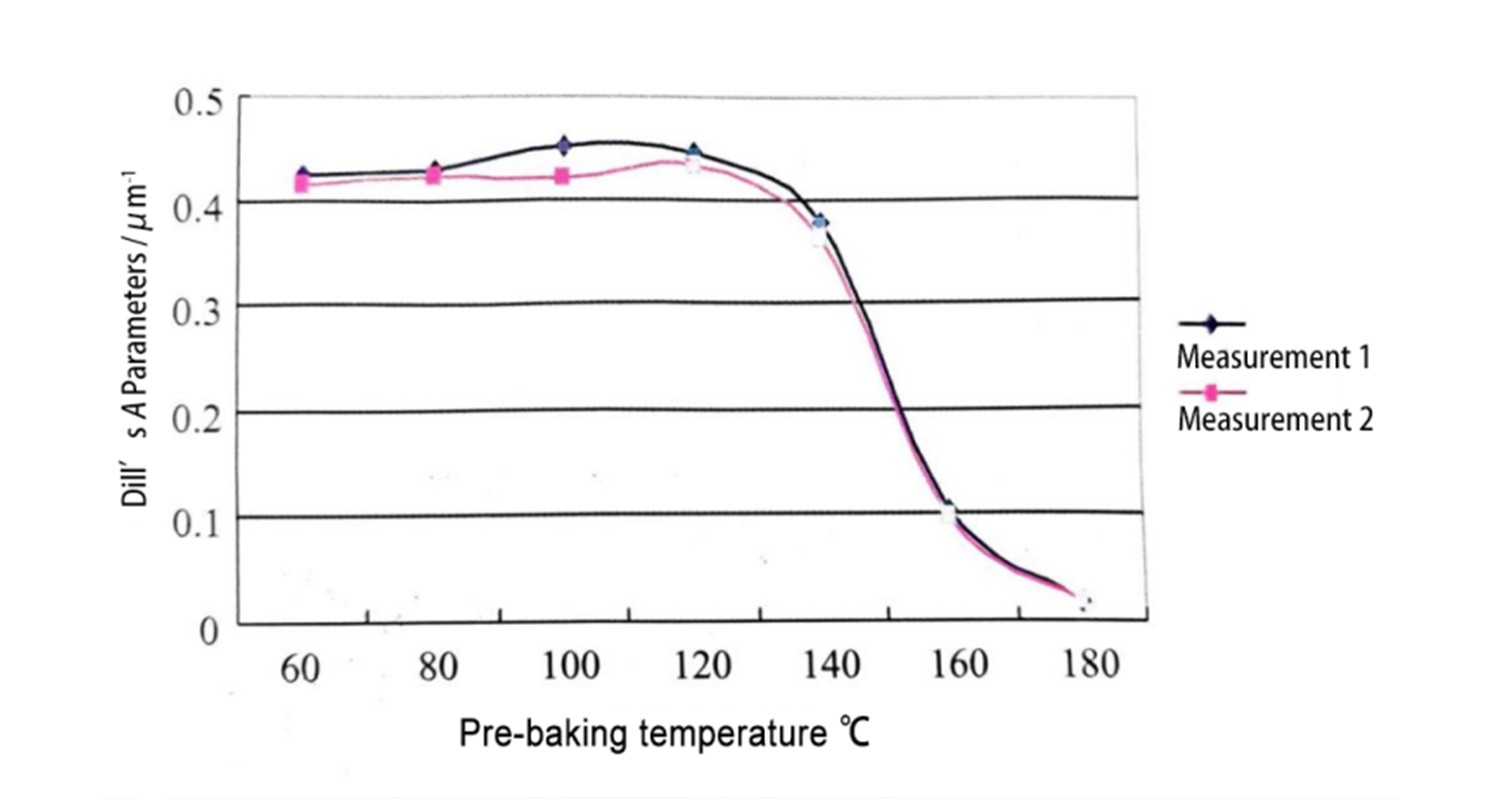
Rysunek 11: Zależność pomiędzy temperaturą przed pieczeniem a parametrem A Dilla
(wartość zmierzona OFPR-800/2)
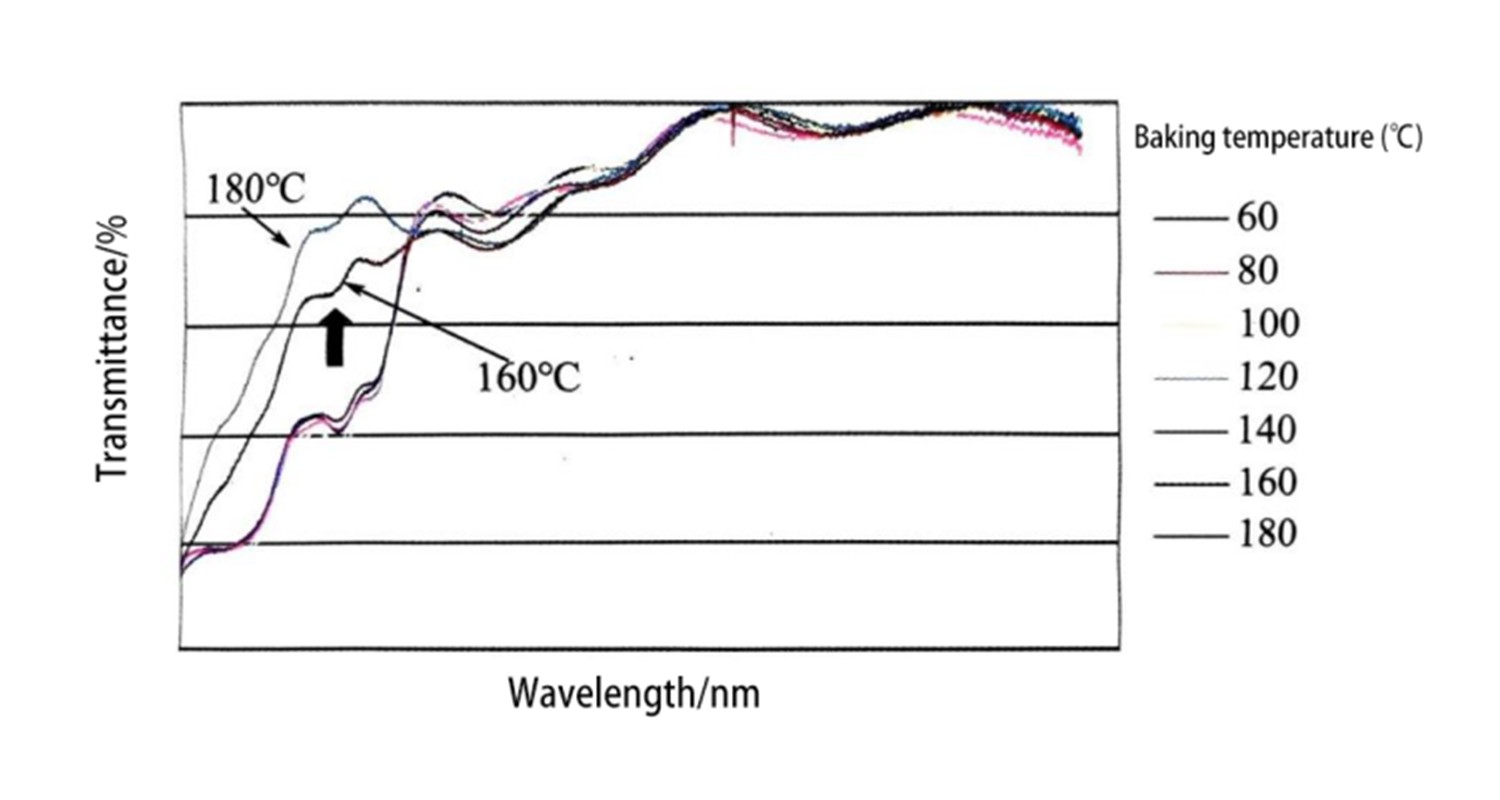
Rysunek 12: Przepuszczalność widmowa w różnych temperaturach przed pieczeniem
(OFPR-800, grubość folii 1um)
Krótko mówiąc, metoda powlekania wirowego ma wyjątkowe zalety, takie jak precyzyjna kontrola grubości warstwy, wysoka wydajność kosztowa, łagodne warunki procesu i prosta obsługa, dzięki czemu ma znaczący wpływ na zmniejszenie zanieczyszczeń, oszczędność energii i poprawę wydajności kosztowej. W ostatnich latach powlekanie wirowe zyskuje coraz większą uwagę, a jego zastosowanie stopniowo rozprzestrzenia się na różne dziedziny.
Czas publikacji: 27 listopada 2024 r